Advancements to PUR formulas and Edgebander Innovations
Published by Rob Young in Edgebanders · Sunday 08 Mar 2020
Tags: Invisible, glue, lines, with, PUR, edgebanders
Tags: Invisible, glue, lines, with, PUR, edgebanders
Advancing PUR Formulas And Edgebander Innovations
While researching PUR glue I came across articles dating back as far as 1996. PUR was new to the edgebanding industry back then and as I read through the article, I found many of the talking points and challenges associated with the use of PUR glue to be the same talking points and associated challenges discussed by shop owners today. Of course, there have been changes to PUR glue formulas and to the gluing systems edgebanders use to process PUR glues, but that information hasn’t filtered down to many shop owners in the North American Market. A much higher percentage of shops in Europe use PUR as opposed to their North American counterparts. There are several reasons for this but three we will look at in this blog
Consumer Demand Drives Our Industry
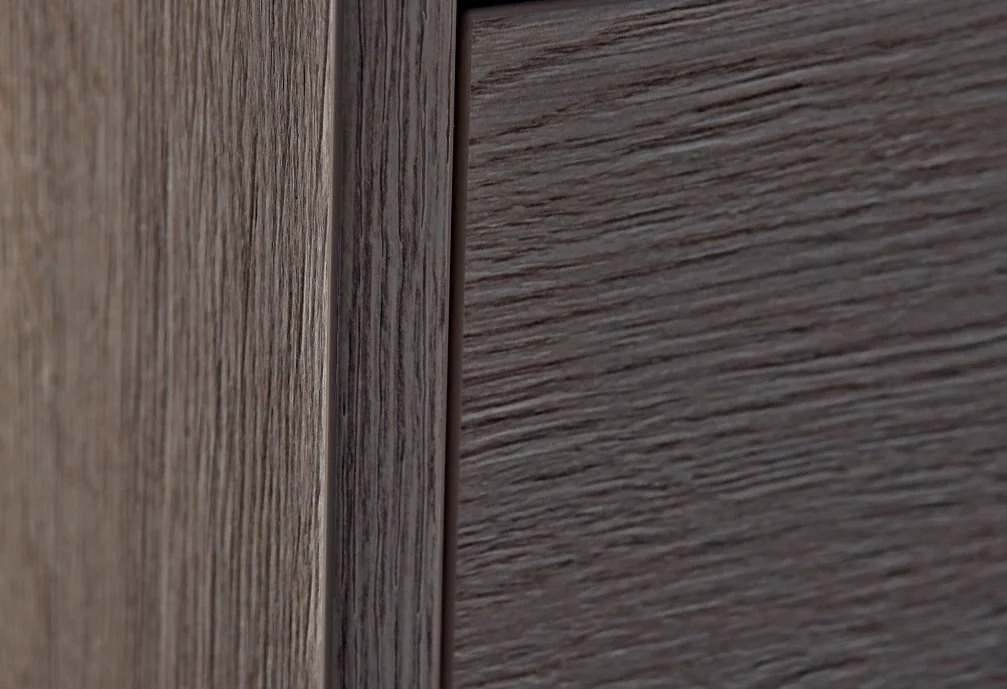
Before we consider the change in PUR glue formulas or innovations to glue pots we need to understand what has driven the changes. Interior designers are creative and love to present possibilities and concepts to consumers. Consumer demand ultimately determines which concepts become trends, but it’s clear, there can only be a demand for a style if the style is presented. NuTek Machinery technicians recently went to the Ott Edgebander factory in Lambach Austria for factory training followed by tours of several large companies in Germany and Austria. It was just as much of a priority for us to view the showrooms at these cabinet companies as it was to view the machinery. We don’t want to offer a machine when working with customers, we want to offer solutions to the challenges they face or will face. Understanding the materials shops work with and the expectations of consumers is key to offering the best possible solution to achieve the desired results. There were of course the standard white, black, and gray cabinets but there were just as many displays with veneer, structured board, and high gloss cabinets. It obvious to me as I install and repair machinery in numerous companies that these product styles are rising in popularity in North America as well. These materials present a challenge to manufacturers as consumers demand better quality for less money. The days of using white glue with white boards and black glue with black boards are coming to an end as consumers are presented with invisible glue line panels. The majority of machinery used in our industry comes from Europe and machinery manufacturers such as Ott have adapted and developed solutions to the challenges faced by cabinet and display companies in their home countries that improve the aesthetics of edgebanded panels while increasing efficiency and profit. These trends them make their way to North America as the machinery to efficiently process the challenging materials is perfected. I started in the woodworking industry 30 years ago in 1990 at large volume producer Merillat Industries. I was told then that the U.S. market trends followed European trends by several years. That isn't to say that European trends will replace the standard cabinet we see on the market today but there are certainly quite a few customers that desire the new styles they see. We may not lag several years behind the European designs for much longer. There are multiple large European cabinet manufacturers currently opening production facilities in the U.S. I’m currently working with one of these larger manufacturers on their dust collection project. They are already in negotiations for their second facility in the U.S. of over a million square feet. American manufacturers are going to need to respond to the consumer demand for the designs these companies bring by improving methods and upgrading machinery to be competitive. Textured, high gloss, and veneer panels require invisible glue lines, and this is one of the driving forces for PUR glue and better processing methods. Don’t panic, much of what you may know about PUR is outdated information. Even a small shop can take advantage of invisible or at the very least, minimized glue lines dependent on the edgebander you choose. Even if your customer base doesn't demand the European style cabinets being introduced, you can still benefit from the innovative machine designs to better process the panels your currently do with the ability to process a wider selection of panels that you may struggle to process now. Not all edgebanders are manufactured equal and the quality of the panel finish, most notably the glue line, attests to this. While some companies argue the necessity of laser or hot air systems for invisible glue lines, we recognize PUR as the best and most versatile option to achieve this. PUR can be used with veneers, HPL, and solid wood edges as well as all the edges laser and hot air can process. PUR is more versatile and can produce invisible glue lines if your pay attention to key features on your edgebander that will allow you to process and achieve this.
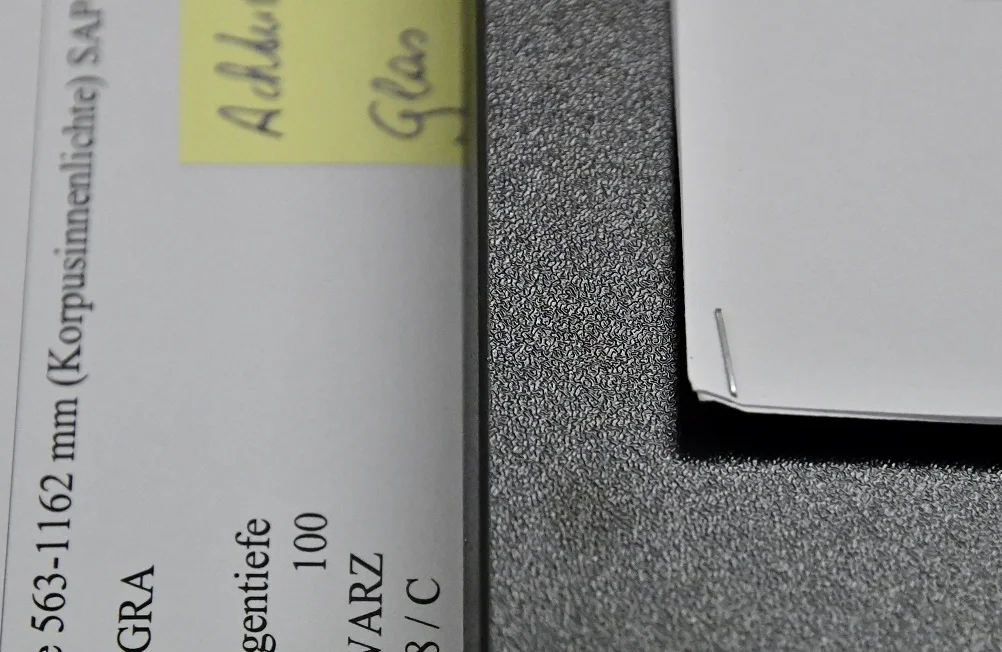
What Is PUR Glue?
- PUR glue is a reactive chemical bond. Moisture in the air, in the panel and in the edge, material initiate the chemical reaction. There is more than enough moisture, even in arid locations, to initiate the chemical reaction.
- PUR is melted and applied at a much lower temperature then EVA glue. Just like EVA, there are several formulas of PUR glues, each with characteristics that determine the application temperature. PUR glues used in straight line edgebanders often operate at temperatures between 120-140 degrees Celsius. In comparison EVA glues often operate in temperature ranges of 180-220 degrees Celsius. If you’ve ever burnt your hands on a hot pot full of EVA glue you will immediately appreciate the temperatures PUR glues are applied at. The lower temperatures also benefit edgebanding tapes that are temperature sensitive that can melt and distort at higher temperatures.
- PUR won’t delaminate at higher temperatures. Once PUR is applied and cures it can’t be remelted.
- PUR is waterproof. This makes PUR a perfect choice for outdoor use or areas near sinks.
- PUR forms a watertight bond. This is an important selling point to hospitals and medical offices. The waterproof bond won’t allow bacteria to grow in cracks and crevices.
- PUR requires a much thinner application then EVA glues. With the proper edge presentation, best achieved with diamond premill tools, PUR glue can result in a minimal to invisible glue line. This quality and visibility of the glue line is determined by the gluing system of the edgebander.
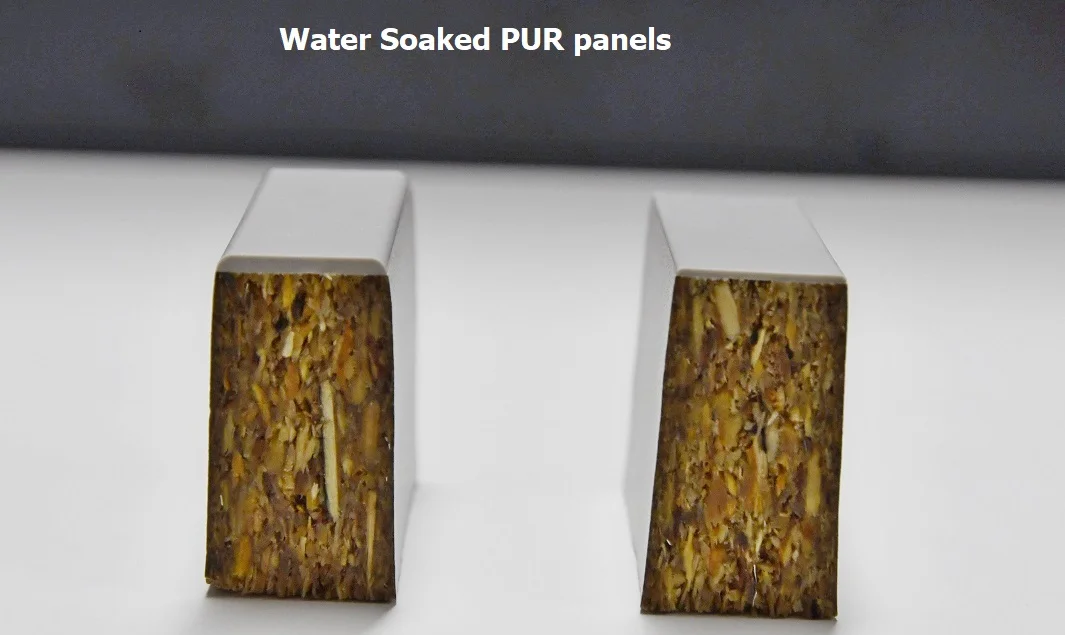
PUR Myths
There are numerous reasons for you to consider the use of PUR glue but let’s start by addressing some of the objections to PUR glue. Many of the objections to PUR glue in an edgebander date back to the earliest days of PUR being introduced into the market. I recently read an article from 1996 discussing the difficulty PUR glue can present in the machining process. I hear the same objections regarding PUR today as were outlined in the 1996 article. The PUR formulas and edgebander systems that process PUR have come a long way since then. When you take the fear out of using PUR you can begin to see the many benefits. Here are a few of the outdated objections.
1. We have a small shop that only used our edgebander for a few hours at a time. If you use your edgebander once a month PUR isn’t a good fit for you but a few hours at a time won’t negate your ability to use PUR and in fact I might argue a few hours a day makes it even more attractive to use PUR over EVA. Each time you heat up and cool down EVA it loses strength and becomes discolored and even burnt. Soon you will find your EVA glue pot looks something like this one. A properly maintained PUR glue pot won’t require scraping the pot. PUR is available in sealed packages of smaller quantities. The PUR glue once heated will need to be properly stored to ensure the glue doesn’t cure and harden in the pot. There are several methods for storing PUR glues once they have been heated. Dry boxes remove moisture from the air and allow previously heated PUR to be stored for several days without hardening.
2. PUR glue pots require daily cleaning. This is of course no longer the case. Ideally you don’t want to fill the glue pot hopper completely full if you only need to run for a short period of time. If you do have glue left over at the end of the day, the pot can be stored in a dry storage system for use the following or even several days later.
3. PUR pots are difficult to clean. This depends on the brand of edgebander you select. The PUR Combimelt service station supplied with Ott edgebanders is much easier to clean than an EVA glue pot. The combimelt system is the answer to edgebander operators’ dreams. Follow these simple steps and see just how easy it is to clean the Combimelt system.
a. Empty excess glue from the PUR hopper and pot.
b. Place the Combimelt pot and hopper on the service station.
c. Empty Jowat cleaning solution into the pot and hopper
d. Plug the pot and hopper into the storage and service station.
e. Heat the pot up
f. Wait two hours, wipe the residue from the pot.
g. The glue pot is clean and is now ready to use.
4. PUR glue is expensive. PUR glue may be more expensive pound to pound then EVA but, PUR requires less glue be applied to the panel edge. The thinner glue line balances the cost between PUR and EVA.
Machine Innovations
There are many edgebanders available on the market today. Most of these brands are very basic machines with glue application systems that still cater towards EVA glue application. PUR manufacturers have made it possible to use some of their formulas in these basic gluing systems but you should avoid these systems when applying PUR glue. Glue pots that are designed for EVA will require constant cleaning. Insufficient cleaning will endanger your glue pot. It’s also important to understand many of the EVA glue pots don’t utilize the proper knurl pattern on the application roller to achieve an invisible glue line when used with PUR glues.
There are still large gaps among the edgebanders that are manufactured for PUR usage. There’s a huge difference between running PUR glue and effectively utilizing PUR glues to recognize all the benefits PUR glue has to offer. Certainly, there are benefits to the waterproof properties of PUR, the heat resistance and the watertight seal at the glue line that make PUR an excellent choice in many applications. If you plan to use PUR for the above reasons, it’s a small step to take to choose the correct machine that will also allow you to experience the benefits of an invisible glue line. The design of the glue pot and the premill station are critical to achieving an invisible glue line. The aesthetics of your finished panels begins with the presentation of the proper edge. Wavy or chipped edges will never give the appearance of an invisible glue line regardless of the glue system your edgebander has. The majority of edgebanders on the market, even those that have made design allocations for PUR glue aren’t capable of invisible glue lines and quality edge finishes year after year. Some of this is due to design flaws or light weight construction that appear as the machine ages. Wear is certain to occur to key components of edgebanders that affect edge processing and glue dosages in machines that lack true quality in their designs and manufacturing. Ott edgebanders lead the industry with their innovative designs that make PUR usage practicle for shops of all sizes. Even smaller shops can now compete with larger ones by presenting quality edges with invisible glue lines. We were told by one Ott technician that the last EVA glue pot machine he installed was four years ago in 2016. If you understand the importance of positioning your company in the marketplace with an edgebander that processed PUR glue than you should consider the following key features when purchasing a new edgebander.
Precision Control. I have repaired and serviced edgebanders for over 30 years now. Over those 30 years I have achieved a high level of proficiency adjusting glue lines and workstations to achieve properly machined edges, but times change and methods improve. In the battle for a perfect edge and invisible glue line even a tenth of a millimeter counts. There are variances to the thickness of edgebanding that can frustrate a conscientious shop owner or operator. Servo controlled workstations and glue pots can eliminate manual adjustments to the machine by operators. Differences in panel construction requires fine tuning to the glue line to achieve the invisible glue line that consumers are becoming aware of and beginning to demand. Servo and stepper-controlled workstations reduce set up times and allow for the finest increment adjustments possible. Control of panel machining and glue dosage is critical to achieving an invisible glue line and flawless edges on panels. There are two key components of an edgebander that determine your success in achieving an invisible glue line. I can’t address every machine and the processes every manufacturer uses. I’ll be referring to the Ott edgebander design and methods below. NuTek Machinery has decided to partner with Ott in the U.S. because of their high-quality construction and efficient edgebanding process. Ott focuses on edgebanders and have designed machines with little to no setup times that are the easiest to maintain on the market. Ott edgebanders are surprisingly affordable for even a small shop. Larger machines, with robotic arms and stacking stations give larger shops the edge on their competitors. Servo controls and glue stations are utilized in every model Ott offers. Read about the key features necessary to achieve an invisible glue line below and research other manufacturers to compare to the Ott line-up.
1. Premills. You can achieve clean cuts with beam saws and CNCs, but the edge supplied by a quality built premill station that utilizes diamond tooling is superior and in the quest for an invisible glue line, every factor counts. Precision servo-controlled adjustments and parameter-controlled tooling radiuses guarantee Ott edgebanders provide the cleanest and most precision sized panel edges in the market. Don’t underestimate the importance of the quality of the edge you are applying edgebanding to.
2. Glue line dosage. The thickness of the glue line is critical to achieve an invisible glue line. If you apply to much glue not only will a glue line be visible, but you will also have the same issues in workstations that follow the glue pot that you have on an EVA edgebander. Glue that can potentially clog dust collection ports, coat tooling, and clog buffing wheels. PUR continues to react with moisture for up to 5 days till fully cured. It becomes extremely difficult to impossible to clean or remove. The proper glue dosage is critical to achieving an invisible glue line and maintaining your edgebander. Ott edgebanders require no manual adjustments by the operator to adjust the thickness of the glue applied. The glue line is adjusted via the touch screen monitor or in prewritten programs. The advantages to writing programs or making the slightest of adjustments to the glue dosage via the touch screen or barcodes is clear. For example, when switching from particle board to MDF it becomes necessary to adjust the glue dosage in order to maintain an invisible glue line. While particle board consists of gaps in the core, mdf board is condensed and smooth. adjustment to the application thickness of the glue is necessary to maintain an invisible glue line. This is done automatically or with the touch of a button with the Ott Combimelt system. A stepper motor rotates the glue dosage rod with precision. The Combimelt system is patented and only available on Ott edgebanders. Even the finest of details was given consideration when designing it. The glue pot is driven from above. You won’t deal with shafts and seals from the bottom of the glue pot. You’ll never have to worry about PUR leaking onto universal joints or chains. The glue pot is removed and stored in less than a minute. The service station allows for the glue pot to be preheated for use or cleaned without effort. You can learn more about the combimelt system by contacting NuTek Machinery via email, phone, or the information request form.
New trends and designs in the industry are going to force PUR into shops that want to maintain or grow their market share. It would be our pleasure to assist you in making the change or improving on your current process to give you the competitive edge you’re looking for.
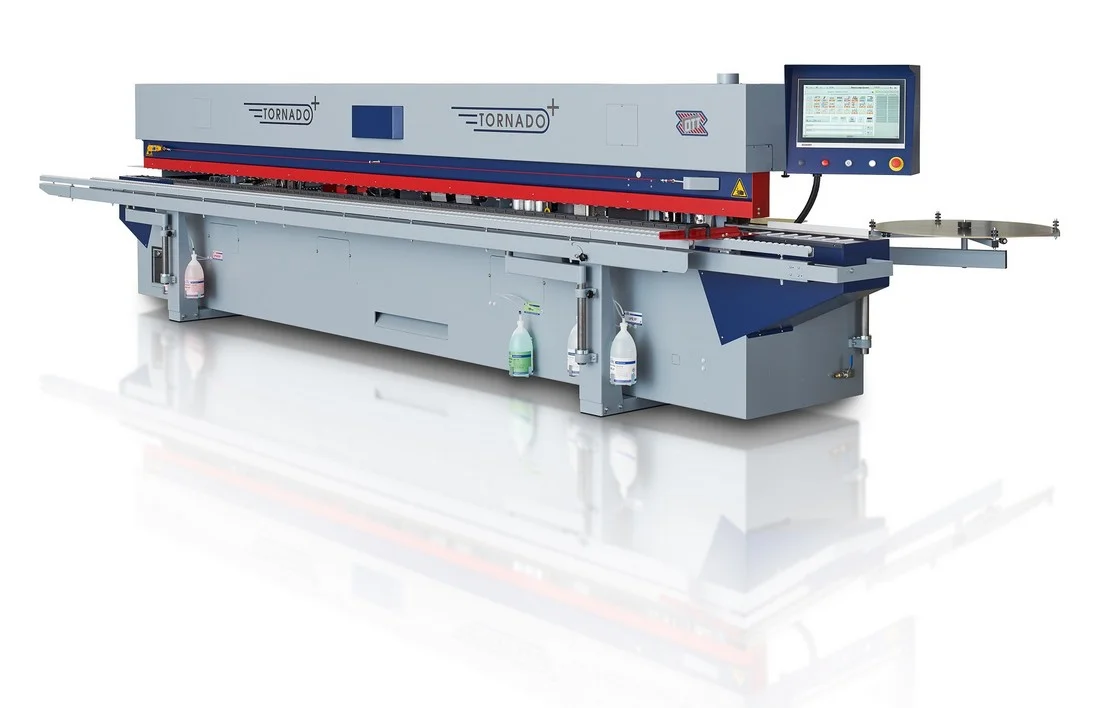